Did your manufacturing organization implement Microsoft Dynamics 365 Finance and Operations a few years ago? Have you since lost focus on unlocking additional business value? It might be time to form new strategies for innovation and explore new opportunities specific to the manufacturing sector.
In this article, we highlight relevant areas to consider. First, let's dive into some background information.
Back in 2016, Microsoft revolutionized the enterprise ERP landscape by bringing Microsoft Dynamics AX to the cloud, transforming it into Microsoft Dynamics 365 Finance and Operations. Fast forward a couple of years, and Microsoft introduced the Evergreen approach, a game-changer designed to keep all customers on the same version with continuous upgrades. This move not only fostered continuous innovation but also significantly enhanced customer service.
Then, in 2020, Microsoft divided Dynamics 365 Finance and Operations into two distinct solutions: Microsoft Dynamics 365 Finance and Microsoft Dynamics 365 Supply Chain Management.
If you were among the early adopters of Microsoft Dynamics 365 Finance and Operations, you're likely well-acquainted with managing the lifecycle of an Evergreen solution by now. Reflecting on this journey, your business is still running on a cutting-edge, up-to-date solution years later. This continuous innovation is one of the standout benefits of modern cloud solutions, ensuring your business remains agile and ahead of the curve.
What happened after the implementation project was done?
In my experience from previous projects in the manufacturing sector, implementing an ERP solution is often a huge task. It has a significant impact on both the business and the organization, requiring immense commitment and effort from everyone involved. I have often witnessed that organizations feel a bit worn out after go-live. Naturally, the focus shifts from innovation to simply operating the business.
This shift often leads to a loss of focus on unlocking additional value with the solution, and things that were scoped out of the project may not be addressed. Meanwhile, the solution continues to evolve, and new opportunities specific to the manufacturing industry become available, which may go unrecognized. Sooner or later, it’s vital to change focus again and begin to form strategies for unlocking new value with the solution.
Where is the potential?
A crucial question to ponder is, where can you uncover new value in your manufacturing operations?
From my perspective, Dynamics 365 Finance and Dynamics 365 Supply Chain Management are robust solutions brimming with features that can streamline and enhance numerous manufacturing processes. These capabilities are built-in and accessible to all customers. However, when the focus is primarily on day-to-day production, many are unaware of the potential within the solution they have implemented.
Drawing from our experience in the manufacturing sector, we have identified several functional areas that are often overlooked but can significantly improve operational efficiency and unlock value.
Use the information below as a source of inspiration for areas to explore in collaboration with your partner.
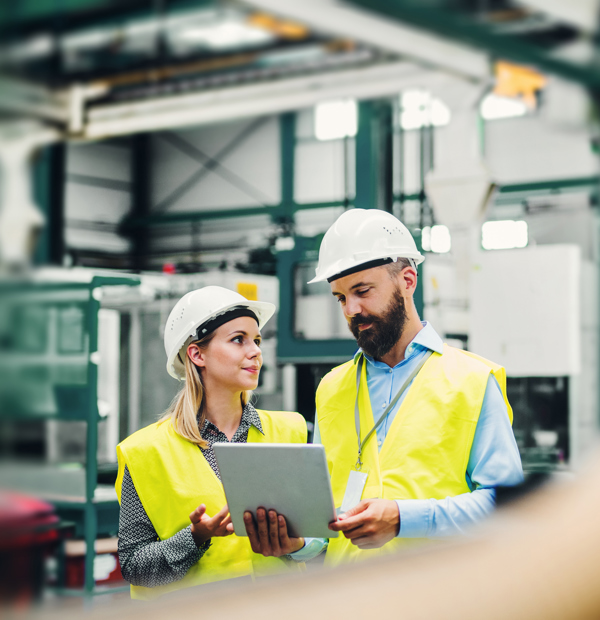
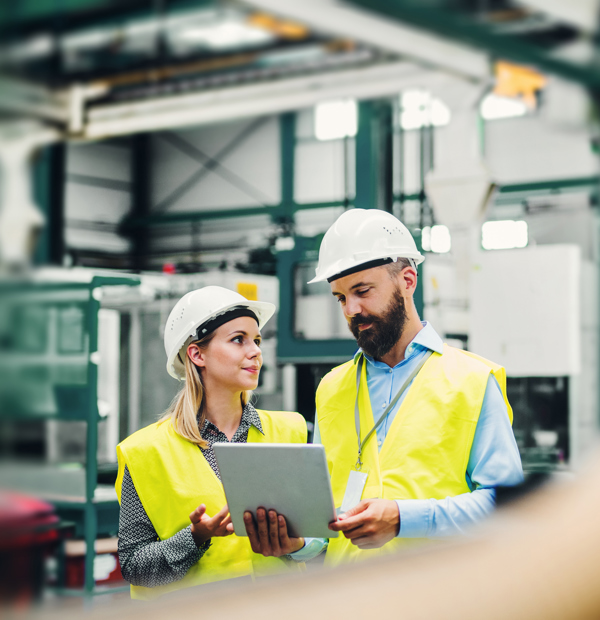
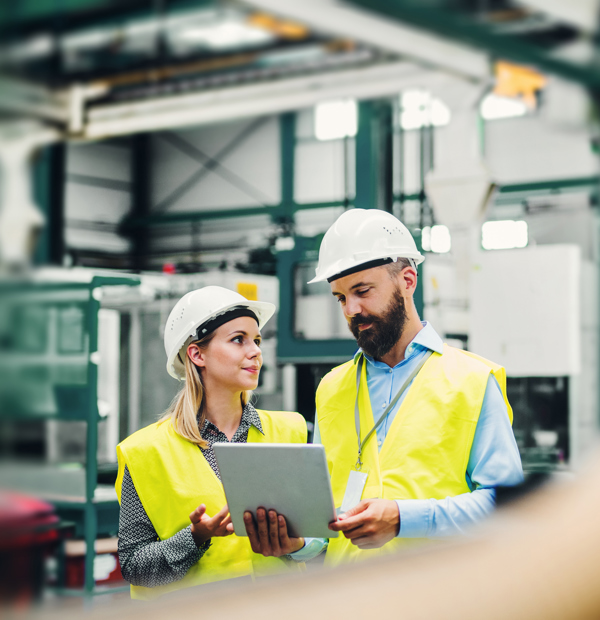
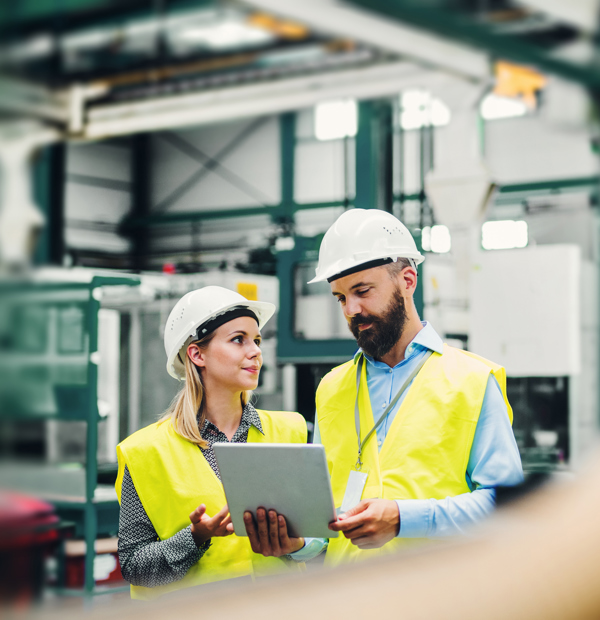
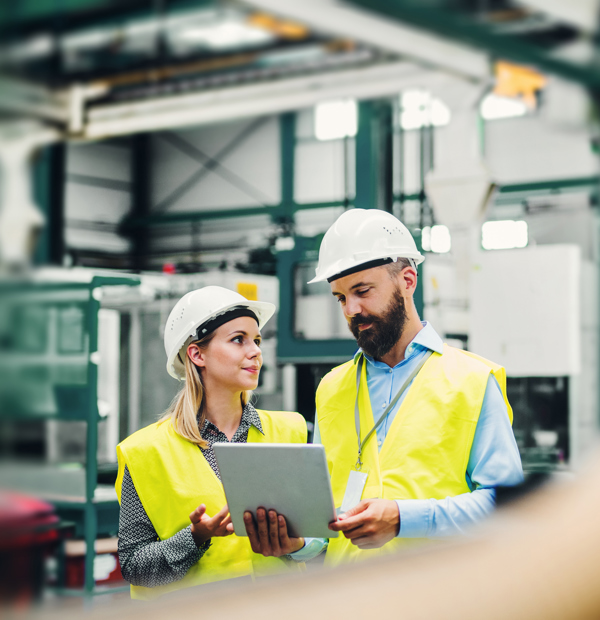
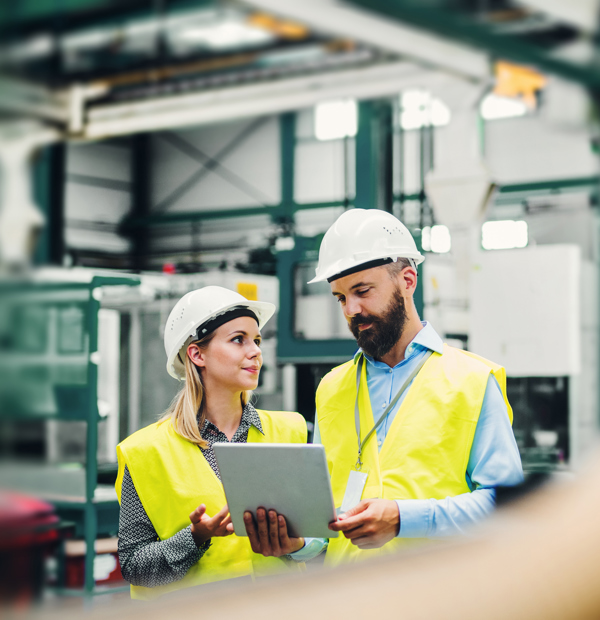
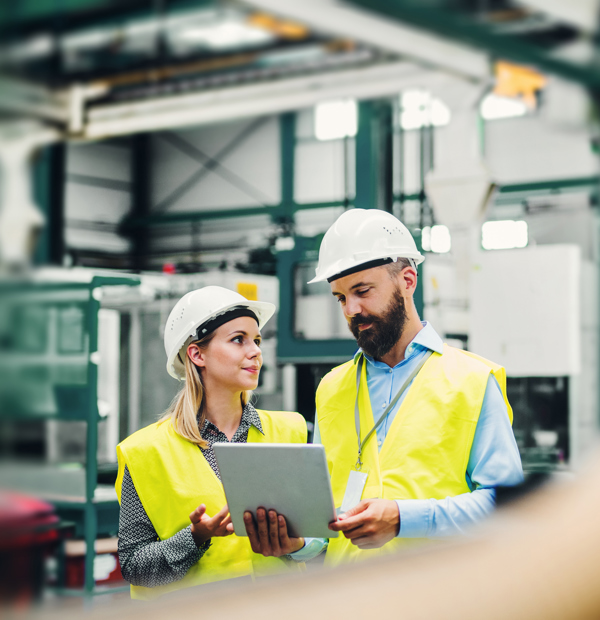
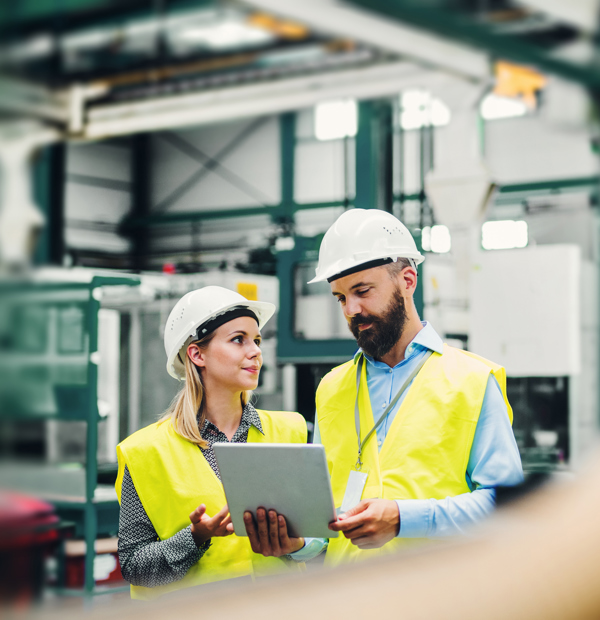
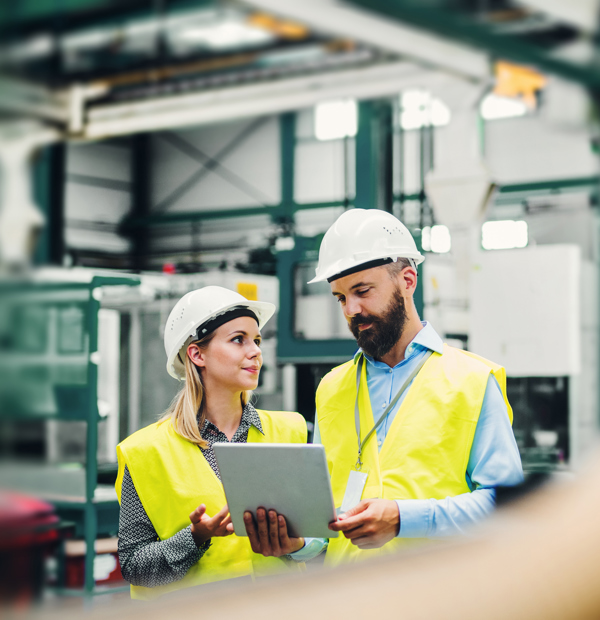
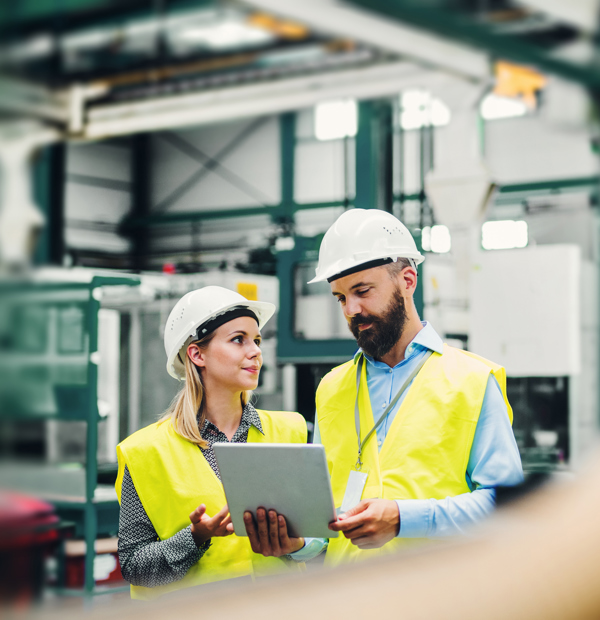
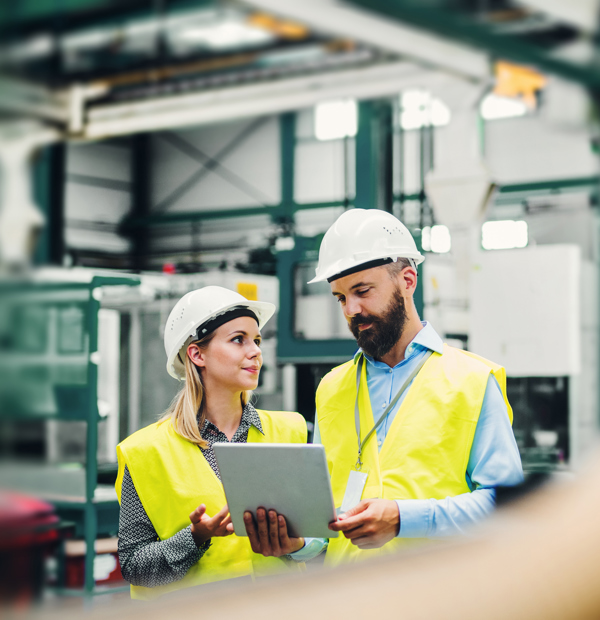
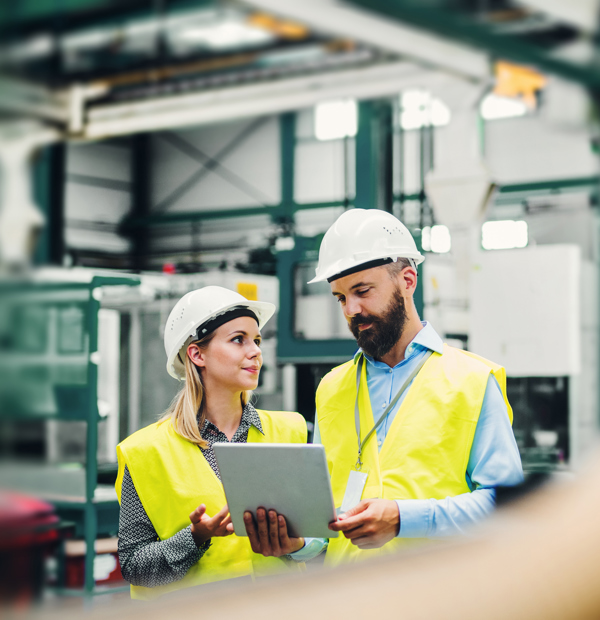
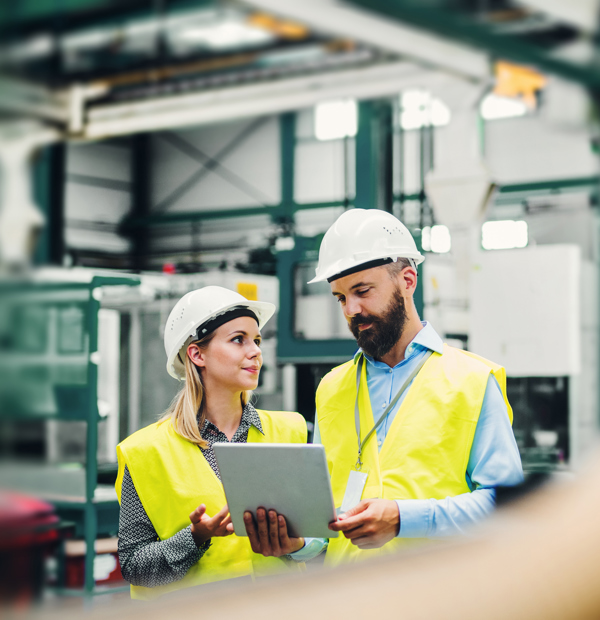
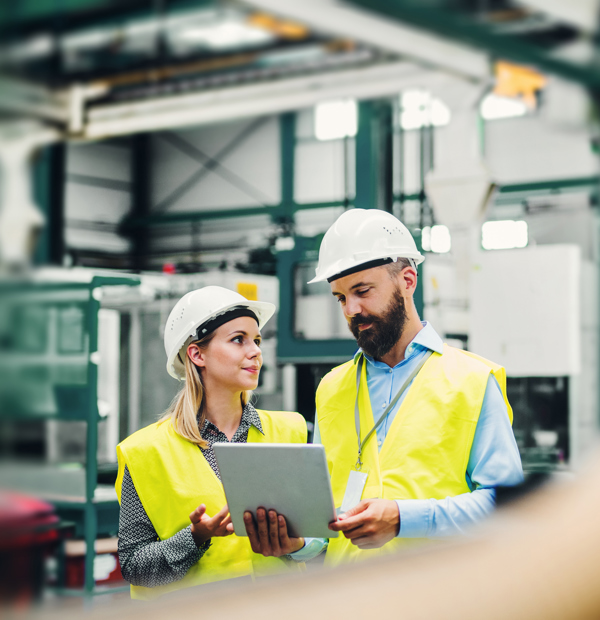
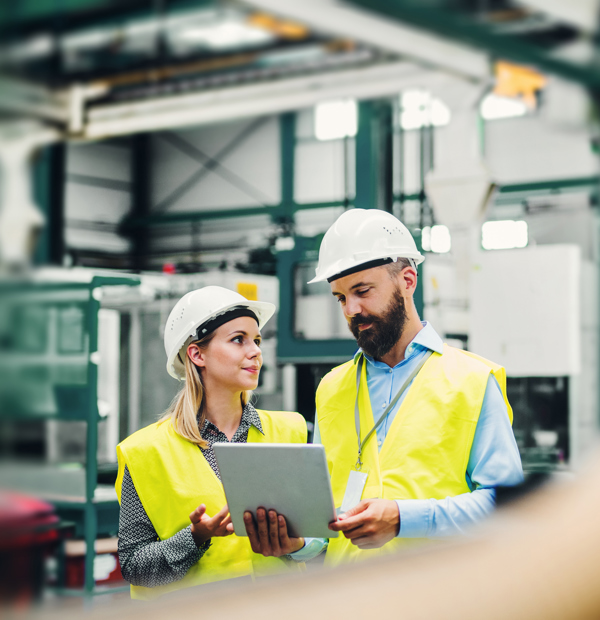
-
Minimizing downtime of equipment is critical for business performance. Asset management includes capabilities for managing and maintaining inhouse assets. It integrates with modules like project accounting, procurement, and HR, enabling reactive and preventive maintenance. It also supports predictive maintenance with IoT and advanced analytics, and features a mobile app for maintenance work.
-
Many businesses explore adding recurring revenue for benefits like predictable income and brand loyalty. Subscription Billing manages the entire subscription lifecycle, supporting various billing models and automating revenue recognition. It provides detailed reporting and integrates with other Microsoft Dynamics 365 Finance components for smooth data flow.
-
Purchase requisitions are used to request goods or services. Employees can select items from a catalogue or request non-catalogue items. Requisitions go through an approval workflow and are converted into purchase orders for vendors. This ensures authorized and tracked purchases, managing procurement efficiently.
-
Vendor collaboration allows vendors to manage purchase orders and requests for quotations directly in your system. Vendors can review, accept, or request changes to orders, ensuring clear communication. The portal provides limited access to vendor contacts, enhancing relationships and procurement efficiency.
-
Invoice capture automates the accounts payable process using OCR and RPA. Employees scan invoices, OCR extracts data, and the system matches invoices with purchase orders. It identifies exceptions and updates financial records, routing invoices for approval through workflows based on data and amount.
-
Engineering Change Management introduces structure to product data management, enabling controlled procedures for defining, releasing, and revising products. It manages product versioning and lifecycle changes, supporting engineering change requests and orders through workflows for proper approval and implementation.
-
Demand-Driven MRP (DDMRP) decouples supply and demand by placing inventory buffers at key points in the supply chain. These buffers mitigate the "bullwhip effect" and use dynamic adjustments to respond to changes, ensuring optimal inventory levels and enhancing supply chain efficiency. DDMRP requires Planning Optimization.
-
Warehouse management only mode lets you set up a legal entity dedicated to warehouse management processes. This entity can provide warehousing services to other legal entities or external ERP systems, ensuring efficient warehouse operations.
-
MES (Manufacturing Execution System) integration enables seamless data exchange between Microsoft Dynamics 365 Supply Chain Management and third-party MES solutions. It ensures real-time synchronization of production data, eliminating manual data entry, and includes a dashboard for monitoring event processing history.
-
Material Handling Equipment Interface (MHAX) enables integration between Dynamics 365 Supply Chain Management and external material handling systems. It facilitates real-time data exchange, allowing automated warehouses to process work generated in the Warehouse Management module, ensuring smooth communication.
-
Project management and accounting supports project planning, execution, and analysis, tracking resources, schedules, and costs. It provides detailed project accounting, including cost tracking and budgeting, ensuring financial control. It integrates with other Dynamics 365 modules for comprehensive project oversight.
-
Credit and collections manage customer credit limits and collection activities efficiently. It allows setting credit limits, assigning risk scores, and creating blocking rules. The module offers a centralized view for managing accounts receivable, tracking overdue invoices, and processing write-offs.
-
Microsoft Dynamics 365 Human Resources manages and optimizes HR processes across an organization. It automates tasks throughout the employee lifecycle, including hiring and performance management. It provides tools for tracking employee development and compliance, and offers self-service capabilities for employees.
-
Configurable business documents allow users to customize and generate documents using Word and Excel templates. The feature uses the Electronic Reporting (ER) framework to create and manage templates, allowing users to modify layouts and apply complex formulas without coding.
Embracing continuous innovation for cloud success
In my experience, to be successful in the cloud requires a fundamental shift in the organizational mindset.
The organization must be ready to embrace change quickly and effectively. I strongly believe this involves continuous work on strategies to maximize the return on investments. It’s also crucial to collaborate closely with your Dynamics 365 partner to align strategies and uncover new potential within the solution and platform.
By establishing a process for continuously exploring and evaluating new opportunities, your manufacturing organization can remain agile, innovative, and ahead of the competition.
-
Jerker Carlström
Manufacturing Industry Lead, Cepheo
Jerker Carlström is a Dynamics 365 Platform Architect and Nordic Manufacturing Industry Lead with extensive experience in implementing Dynamics 365 solutions. He has a background in Supply Chain Management and guides companies in the manufacturing industry on their digital transformation journey, with a strong focus on building long-lasting relationships and realizing business value.
Contact our Sales Directors for a discussion about your company's digitization.
-
John T. Hummelgaard
Sales Director, Denmark
-
Patrick Bubicic
Sales Director, Sweden
-
Lars Erik Lindhjem
Sales Director, Norway